When admiring a stunning epoxy floor, it’s easy to appreciate the skillful craftsmanship and the way the seamless design elevates the room’s aesthetics. However, the most vital factor in a floor’s performance is the quality of the surface it adheres to. In Florida, we face unique challenges such as soft concrete, cracking, moisture migration, salt intrusion, and more, each capable of undermining a project if not properly addressed. Often, multiple issues can arise simultaneously, necessitating additional care during the surface prep phase to ensure a successful outcome.
The team at Top Coat Epoxy of Central Florida understands that thorough surface preparation is essential for achieving the best results in every project. During a recent multi-car garage job, an extensive multi-step surface preparation process was necessary due to a cream coat on the concrete slab that was compromised by spalls, embedded dirt, and grime.
The Most Vital Factor In A Coatings Success
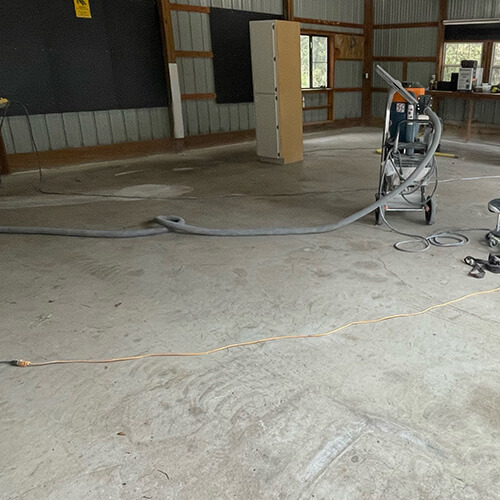
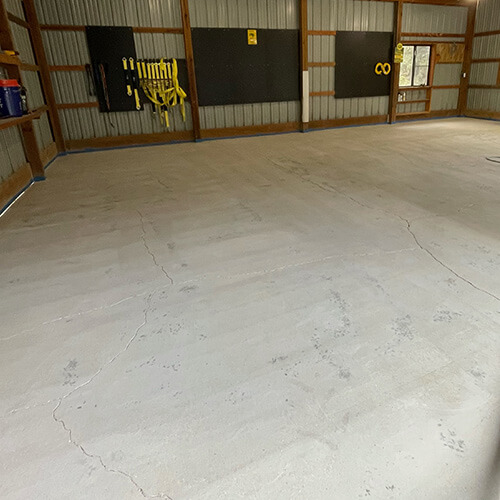
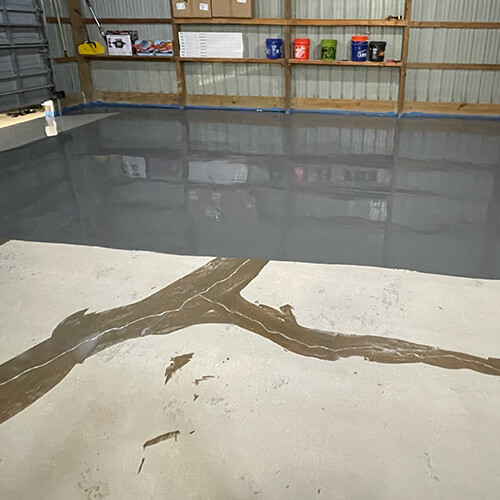
To address this, the TCE team utilized diamond grinding to achieve a Concrete Surface Profile of 2/3, effectively removing the damaged outer layer and establishing a solid foundation for the new coating to adhere to. However, the surface preparation did not stop there. Luis from TCE then focused on rectifying the cracks and addressing moisture migration. His expertise led him to carefully chase out the cracks, creating openings that could be filled with a fast-setting, two-part liquid crack repair solution. After allowing this repair to cure, the team applied a pigmented epoxy to the floor.
This base coat is vital for three key reasons. Firstly, it establishes a strong mechanical bond to the concrete, enabling it to withstand both vehicular traffic and hydrostatic pressure. Secondly, it effectively seals the pores of the concrete, reducing imperfections in the finish coat. Finally, the incorporation of pigment signals to the applicator that the entire floor has been adequately prepared and is primed for the coating application.
Surface Prep Is The Key To A High-Quality Floor
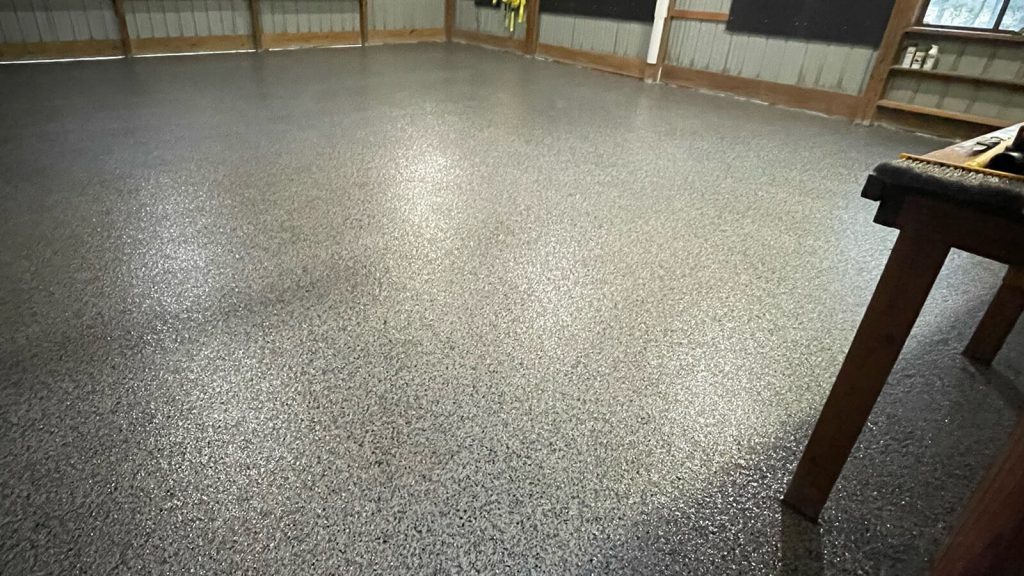
In this project, TCE installed an epoxy flake floor with a top coat, utilizing a resinous pigmented coating. These coatings can be either a Epoxy, Polyurethane, Polyaspartic or a combination. The application process involved coating the surface and immediately broadcasting the flake onto the still-wet material. Once the coating cured, according to the manufacturer’s specified timeline, TCE conducted a thorough inspection to confirm that all flakes had adhered properly. Finally, a clear coat is applied to encapsulate the flake, enhancing the floor’s durability and making it easier to maintain.
When considering a new decorative concrete floor, it is essential to inquire about how the contractor plans to address the necessary surface preparation for your project. The old adage holds true: you get what you pay for, and this applies to all types of concrete flooring. Often, lower prices result from omitting crucial steps in surface preparation and using subpar materials.
Property owners select companies like Top Coat Epoxy because they understand that quality workmanship reflects a solid reputation. The team takes pride in creating and installing durable decorative concrete floors that are designed to endure the test of time.